Example 1
Supply Air Handling Unit with Water Heater (and, Optionally, Water Cooler)
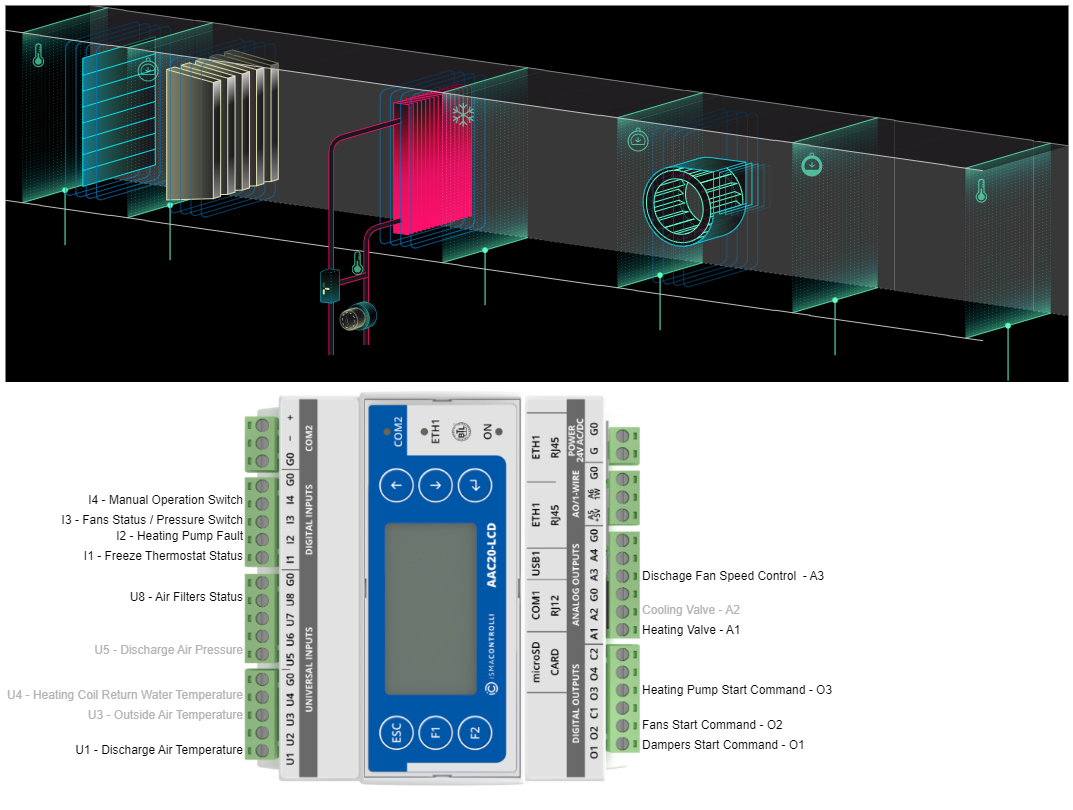
Inputs and outputs configured for supply air handling unit with water heater
The air handling unit consists of:
2-position inlet damper;
air supply filter;
water heater with a valve and a heater pump;
fan controlled by an inverter.
The required sensors/signals are:
discharge air temperature sensor;
anti-freeze thermostat;
fan operating status (pressure switch, signal from the inverter);
manual switch control (permission to operate the ventilation system).
Some of the useful sensors/signals, optional but not required:
heater pump failure status;
filter dirty status (for monitoring only).
In addition, the system can be equipped with optional sensors/signals, such as:
outside air temperature;
heater return water temperature;
discharge air pressure sensor (only when there is a need to maintain constant pressure on the supply duct).
The application allows for:
controlling the opening/closing of the 2-position inlet damper;
the fan to start, controlling its speed (constant or pressure dependent);
controlling the modulating (analog 0-10 V DC) heater valve actuator and the heater pump.
In addition, if a water cooler is also configured, it will be controlled by the modulating (analog 0-10 V DC) cooler valve actuator (here, an outside air temperature sensor is required – i.e., to disable using the cooler in winter).
AHU configuration example:
heater mode – Heater [1]
energy recovery mode – None [0]
cooler mode – None or Cooler [0 or 1] (depending on the need)
humidifier mode – None [0]
economizer mode – None [0]
temperature control mode – Constant Disch Temp [2]
humidity control mode – n/a
Application Algorithm Description
Start-up
The first step after configuring the application for a particular type of the AHU is to make sure that the time schedule is correctly configured, which allows the AHU to run in a normal mode (Plant Mode as Occupied Period [4]) or in a night mode (with reduced efficiency - Plant Mode as Night Cycle [2]). If not, the time schedule must first be set correctly to allow a proper AHU operation.
The signal that allows the AHU to start is the signal connected to the I4 input of the AAC20 (Operating Switch). Activating this signal (physical short circuit at the input) and correctly setting the time schedule allows the AHU to start, while deactivating the signal automatically stops the AHU.
Preheater
The next step before starting the AHU is for the controller to verify that the heater has no active alarm conditions associated with the antifreeze protection procedure.
The antifreeze protection of the heater is used in the winter period (when the outside temperature is lower than the limit set by OAT_FrostProtection (by default, 6°C) with a central hysteresis of 1K).
The basic element is an antifreeze thermostat whose physical setting should be in accordance with or slightly lower than the above limit (e.g., by 1°C). The antifreeze thermostat is connected to the I1 input in the AAC20 controller (Freeze Thermostat Status).
Activation of the antifreeze thermostat (physical short circuit at the input) triggers the antifreeze protection procedure consisting of stopping the AHU (turning off the fan and closing the damper), opening the heater valve at output A1 of the AAC20 (Heating Valve) to the level specified in HTV_FrostProt_ValveUp (by default, 100%), and switching on the heater pump at the O3 output (Heating Pump Start Command) if configured for use by HPU_Enable (by default, active - true).
An additional element of antifreeze protection is the use of a return water temperature sensor connected to the U4 input in the AAC20 (Heating Coil Return Water Temperature). If the antifreeze thermostat is triggered, the setpoint for the return water temperature is raised additionally by the level specified in FEZ_RWT_SptUp (by default, 15K).
When the temperature of the heater rises and the antifreeze thermostat returns to the normal state: in such case, if there is a sensor for the water temperature at the return from the heater, its setpoint will begin to fall at the rate of FEZ_SetupRamp (default 1K/min) to the normal setpoint (calculated on the basis of the outside temperature); if there is no sensor, the valve closes at the rate of HTV_Ramp (by default, 10%/min) to the normal opening state resulting from the current system control.
The heater return water temperature sensor also serves as a high limit for the water temperature in the heater by closing the valve if the temperature specified in RWT_MaxSetpoint is too high (85°C by default).
If the pump is activated in HPU_Enable (active by default - true) and connected to the O3 output in the AAC20 (Heating Pump Start Command), it is switched on with the delay HPU_OnDelay (by default, 5 s) when the heater valve connected to the A1 output in the AAC20 (Heating Valve) opens to 3% or more, and switched off with the delay specified in HPU_OffDelay (by default, 300 s) when the valve is open 1% or less.
In winter, the pump is permanently activated if the outside temperature falls below the OAT_FrostProtection limit (by default, 6°C) with a central hysteresis of 1K and if the antifreeze thermostat is activated.
When using the pump failure signal, which is connected to the I2 input on the AAC20 (Heating Pump Fault), and when the value in HPU_StatusAlarmDelay (by default, 1 s) is set to default, then in the winter period the AHU can be turned off if:
DME_EmergencyStop (deactivated by default - false) is active (set to true),
an alarm is generated on the O2 output of the MIX18 module (Heat Pumps Failure Alarm),
and the pump control output is turned off.
The alarm is automatically reset if the signal at the input is deactivated and the pump and AHU system resume operation (if stopped).
An additional feature to ensure a proper and long-lasting operation of the devices operating the heater is exercising the pump and valve. First, the pump is exercised, then the valve, which, by default, takes place every Sunday at 1am in case they are not in use. The exercise consists of turning on the pump for the time specified in HPU_Pmp_Vlv_Exercise (120 s by default) and then opening the valve to 100% for the same time as above.
Dampers
In winter, when the outside temperature is lower than the limit specified by OAT_FrostProtection (by default, 6°C) with a central hysteresis of 1K and if the return water temperature sensor is used, then, it must reach the setpoint (calculated from the outside temperature) to allow the dampers to open after the time specified in DME_OnDelay (by default, 300 s).
If the return water temperature sensor from the heater is not used, the damper is opened only after the time specified in DME_OnDelay (by default, 300 s), during which the valve is opened according to the HTV_FrostProt_ValveUp parameter (by default, 100%) and drops at the rate specified by HTV_Ramp (by default, 10%/min) to the normal opening state resulting from the current system control.
When the outside temperature is above the limit specified in OAT_FrostProtection (by default, 6°C) with a central hysteresis of 1K (summer period), the damper is opened without the delay specified in DME_OnDelay (by default, 300 s) and the heater return water temperature is not controlled at that time.
The damper connected to the O1 output in the AAC20 (Dampers Start Command) opens after the time specified in DME_OnDelay (by default, 300 s) only after the permission from the normally operating heater, and then the signal from the damper is transmitted as a start permission for the fan with a delay of MAD_RunTime (by default, 150 s).
Fans
If a pressure sensor is connected at the U5 input in the AAC20 (Discharge Air Pressure), the fan is controlled smoothly connected at the A3 output in the AAC20 (Discharge Fan Speed Control) in the range from FSC_MinSignal (by default, 30%) to FCS_MaxSignal (by default, 100%) so as to maintain the set pressures. Otherwise, if no pressure sensor is connected, the fan is controlled manually with the set speed in above (higher control value is selected).
The fan has its preset DischPressSpt pressure (500 Pa by default), which it is supposed to maintain by adjusting its speed accordingly.
The fan connected to the O2 output in the AAC20 (Fans Start Command) starts with the delay specified in FSC_OffOnDelay (by default, 5 s) after receiving a permission from the damper.
After receiving the startup permission, the fan speed control signal slowly ramps up at the rate of FSC_Ramp (by default, 1%/min) to the desired value resulting from the corresponding control as indicated above. The rate of rise or fall of the control signal is determined by the same speed.
The pressure setpoint behaves similarly, which during the AHU startup ramps up from zero to the desired setpoint at the speed of DSP_PressSptRamp (by default, 50 Pa/min). If it is changed during a normal operation, it will correspondingly start falling or rising at the same speed specified in DSP_PresSptRamp (by default, 50 Pa/min).
For a night mode, the set pressure is reduced by multiplying it by the DSP_NightReduce factor (by default, 50%).
To protect the fan operation, a fan confirmation signal is connected to the I3 input in the AAC20 (Fans Status/Pressure Switch), which if not activated by the time FDP_BeltAlarmDelay (default 120s), then, an alarm is generated on the O1 output of MIX18 (Fans Failure Alarm) and this causes the AHU to stop. This function can be disabled by setting the zero value in FDP_BeltAlarmDelay (by default, 120 s).
In the automatic reset mode specified in FSC_ManualReset (by default, false), after an alarm from the fan, the alarm will be reset and the AHU will resume operation, while after three unsuccessful attempts to start, the system stops and in the automatic mode it can be reset by removing and reactivating the I4 input in AAC20 (Operating Switch). While if the manual reset mode specified in FSC_ManualReset (deactivated - false by default) is set to true, after an alarm from the fan, the AHU will be stopped and the controller will wait for a reset signal activated by the input connected to the I5 input in MIX18 (Reset), and only then will it attempt to restart the AHU.
Control
In winter, during the AHU startup, the temperature control system temporarily raises the setpoint for the discharge temperature by an additional value specified in DAT_SptRamp (by default, 1K) which drops in time specified in DAT_SptDecTime (by default, 600 s).
For proper operation of the TempCtrlMode temperature control function, select mode 2 as described below.
The fixed-value temperature control function consists of adjusting the discharge air temperature connected at the U1 input of the AAC20 controller (Discharge Air Temperature) based on the set TempSpt temperature (by default, 22°C), and based on the control loop the control level for the heater or cooler is calculated.
If the discharge air temperature falls below the low limit, the cooler is gradually closed, and then the heater starts to open.
If the discharge air temperature rises above the high limit, the heater is gradually closed, and then the cooler starts to open.
The TempSpt temperature setpoint (by default, 22°C) can take into account the winter compensation specified by the WC_DischSptRaise parameter (by default, 4K) or the summer compensation specified by the SC_DischSptRaise parameter (by default, 4K).
In summer, if the outside temperature rises above the OAT_HeaterLimit (by default, 20°C), heater control is blocked, and in winter, if the outside temperature falls below the OAT_CoolerLimit (by default, 14°C), cooler control is blocked.
When the antifreeze protection is triggered, all control signals are reset except for the signal for the heater which is set to the level specified in HTV_FrostProt_ValveUp (by default, 100%). When the risk of freezing ceases, all signals return to normal operation.
The heater valve is opened or closed by the valve actuator according to the control signal coming from the temperature control system according to the configured TempCtrlMode (in mode 2).
Cooler
When cooling is needed, the cooler valve connected to the A2 output (Cooling Valve) opens based on a signal coming from the temperature control system.
The control of the cooler valve is blocked below the OAT_CoolerLowLimit temperature (by default, 14°C) with a central hysteresis of 1K.
During the AHU startup and each time the valve is opened from zero, the control signal gradually increases at the rate specified in CCV_VlvRamp (by default, 5%/min).
To protect against too low air temperature behind the cooler, it is possible to use a temperature sensor connected to the U3 input on the MIX18 module (Cooling Limit Air Temperature) causing the cooler valve to gradually close when the temperature drops to the LIM_Setpoint value (by default, 14°C).
An additional feature to ensure a proper and long-lasting operation of the cooler is exercising the valve. It is carried out by default every Sunday at 1am in case it is not being used. Exercise consists of opening the valve to 100% for the time specified in CCV_Vlv_Exercise (120 s by default).
Electrical Connections
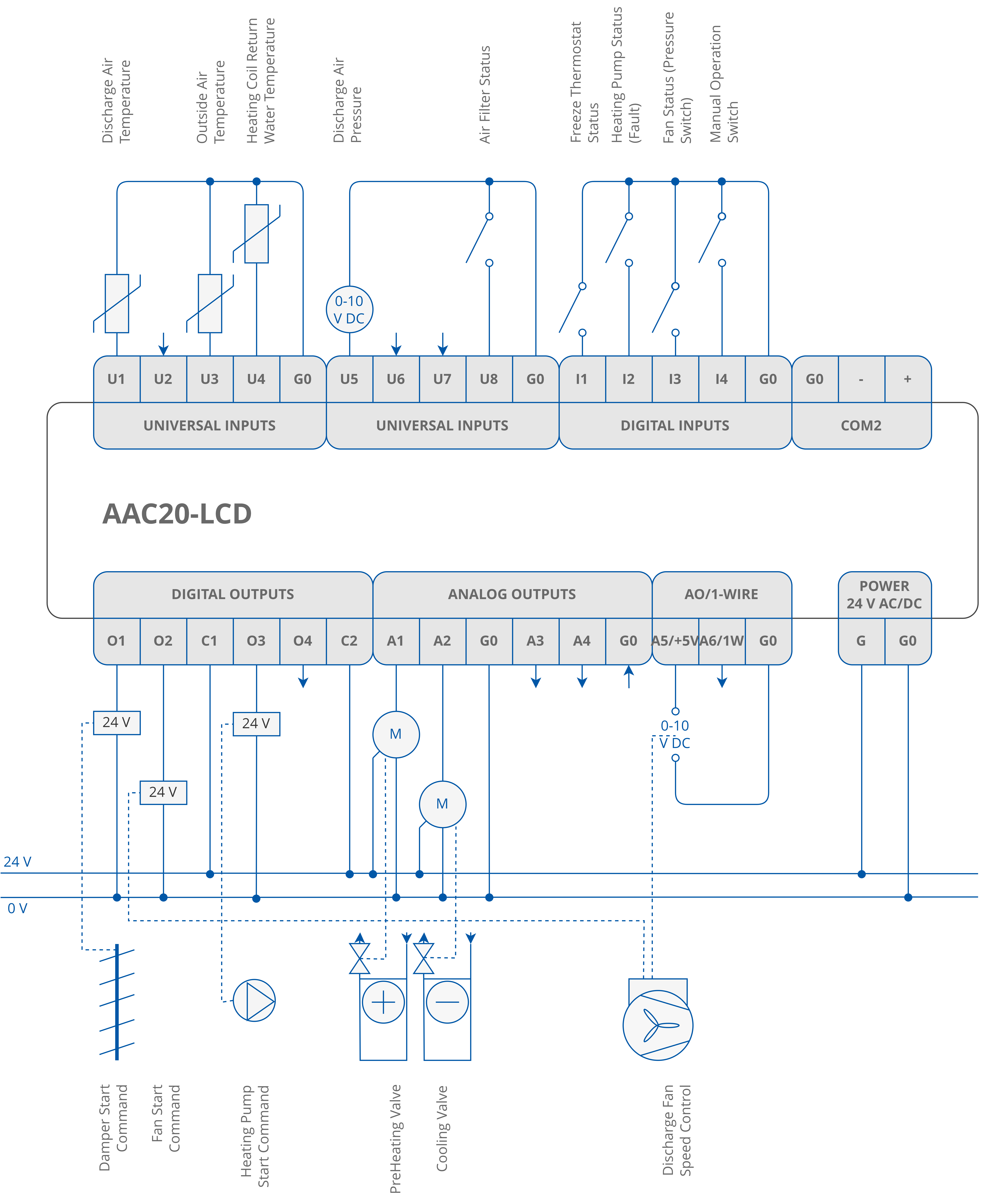
Electrical connections for supply air handling unit with water heater